IoT Advancements in Industry 5.0: Bridging the Gap Between Humans and Machines
May 23, 2024
Blog
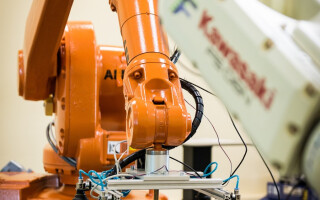
The concept of Industry 5.0 is emerging as a transformative force in the manufacturing sector, where the focus shifts from the automation-centric Industry 4.0 to a more human-centric approach.
Industry 5.0 envisions a future where smart machines and humans work together in harmony, leveraging the advancements in Internet of Things (IoT) technology to enhance efficiency, productivity, and customization in manufacturing processes.
Industry 4.0 has been characterized by the integration of cyber-physical systems, automation, and IoT in manufacturing. It has brought significant improvements in operational efficiency, data analytics, and smart manufacturing. However, Industry 5.0 aims to take this a step further by emphasizing the collaboration between humans and machines. This next phase of industrial evolution focuses on leveraging human creativity and critical thinking alongside advanced technologies to create more personalized, efficient, and flexible manufacturing environments.
Key IoT Advancements in Industry 5.0
Advanced Sensor Technologies
The foundation of IoT lies in the ability to collect data from various sources through sensors. In Industry 5.0, advanced sensor technologies play a crucial role in enabling real-time monitoring and control of manufacturing processes. These sensors can detect a wide range of parameters, such as temperature, humidity, pressure, and vibration, providing detailed insights into the operational status of machinery and environmental conditions.
For example, in a smart factory, sensors embedded in equipment can continuously monitor performance and predict maintenance needs before a failure occurs. This predictive maintenance approach minimizes downtime and reduces costs, ensuring a more efficient production process.
Enhanced Connectivity and Edge Computing
The rapid advancements in connectivity technologies, including 5G and edge computing, are vital for the real-time data processing capabilities required in Industry 5.0. Enhanced connectivity allows for faster and more reliable data transmission between devices, enabling seamless communication across the entire manufacturing ecosystem.
Edge computing, in particular, brings data processing closer to the source of data generation. This reduces latency and allows for quicker decision-making, which is crucial for applications that require real-time responses. For instance, in a collaborative robotic system, edge computing enables robots to process data locally and respond to changes in their environment instantly, enhancing their ability to work alongside human operators safely and efficiently.
Artificial Intelligence and Machine Learning Integration
AI and machine learning are at the heart of the advancements in IoT for Industry 5.0. These technologies enable the analysis of vast amounts of data collected by IoT devices, transforming raw data into actionable insights. AI algorithms can optimize production schedules, improve quality control, and enhance supply chain management by predicting demand and optimizing inventory levels.
Machine learning models can also learn from historical data to identify patterns and anomalies, improving the accuracy of predictive maintenance and reducing the risk of equipment failure. In a human-machine collaborative environment, AI-powered systems can assist human workers by providing real-time recommendations and decision support, enhancing their productivity and effectiveness.
Human-Machine Interfaces (HMIs)
A key aspect of Industry 5.0 is the seamless integration of humans and machines, facilitated by advanced human-machine interfaces (HMIs). These interfaces allow human operators to interact with machines intuitively and efficiently, leveraging technologies such as augmented reality (AR) and virtual reality (VR).
AR and VR can provide immersive training experiences for workers, enabling them to learn new skills in a virtual environment before applying them in the real world. HMIs can also display real-time data and analytics in a user-friendly format, helping operators make informed decisions quickly and accurately.
Collaborative Robotics
Collaborative robots, or cobots, are designed to work alongside human workers, enhancing their capabilities and improving overall productivity. These robots are equipped with advanced sensors and AI algorithms that enable them to understand and respond to their environment, ensuring safe and efficient collaboration.
In an Industry 5.0 setting, cobots can take over repetitive and physically demanding tasks, allowing human workers to focus on more complex and creative activities. This collaboration not only increases efficiency but also improves job satisfaction and safety for workers.
Impact on Manufacturing and Beyond
The implementation of advanced IoT technologies in Industry 5.0 is not just changing manufacturing processes; it's also setting new standards for operational efficiency, product customization, workforce dynamics, and environmental sustainability. Here’s a closer look at how these changes are manifesting across various dimensions:
Increased Customization and Personalization
In the era of Industry 5.0, the ability to adapt to consumer preferences quickly is crucial. IoT enables manufacturers to shift from mass production to mass customization, allowing for the production of products tailored to individual customer specifications without sacrificing efficiency. This level of customization is particularly significant in industries such as automotive, where customers can select various features that are then manufactured and assembled through automated processes guided by IoT systems. Similarly, in consumer electronics, products can be customized in the final stages of assembly to reflect consumer desires, such as color options or hardware preferences.
Enhanced Efficiency and Productivity
IoT technologies streamline operations by synchronizing equipment and data across the production floor. This integration leads to significant reductions in machine downtime and faster throughput, as IoT-driven machines can communicate to prevent bottlenecks and optimize production flow. In complex manufacturing environments, such as aircraft production, where multiple systems must operate in concert, IoT ensures that all parts are manufactured at the right time and delivered to the right place, minimizing delays and improving overall production efficiency.
Improved Worker Safety and Satisfaction
Industry 5.0 focuses on enhancing the interaction between humans and machines, promoting a safer and more engaging work environment. IoT devices equipped with sensors can monitor environmental conditions and detect hazardous situations, alerting workers before accidents occur. For instance, in chemical manufacturing, IoT sensors can detect toxic gas leaks or unsafe temperature fluctuations and automatically initiate safety protocols. Moreover, by automating mundane and physically strenuous tasks, workers are less exposed to potential injuries and can focus on more skilled and satisfying roles, leading to improved job satisfaction and productivity.
Sustainable Manufacturing
IoT technologies are pivotal in promoting sustainable manufacturing practices. They provide precise control over the use of resources such as water, energy, and raw materials, reducing waste and minimizing environmental impact. For example, in industries like textile manufacturing, IoT systems can optimize water usage throughout the dyeing process, significantly reducing water waste and pollution. Energy consumption in factories can also be dynamically managed by IoT systems to lower peak energy use and leverage renewable energy sources, aligning with global sustainability goals.
Supply Chain Optimization
IoT advancements improve supply chain management by enhancing visibility and responsiveness. Real-time tracking of materials and products through IoT sensors and RFID tags reduces inventory errors and ensures that supply meets demand more accurately. This capability is crucial in sectors like retail and pharmaceuticals, where products must be managed meticulously to avoid overstocking and ensure timely delivery to consumers. Moreover, IoT-enabled supply chains can react dynamically to disruptions, rerouting goods and adjusting production schedules as needed, thus maintaining continuity even in volatile market conditions.
As Industry 5.0 continues to unfold, the role of IoT in transforming manufacturing and broader societal structures cannot be overstated. By harnessing the power of advanced IoT technologies, industries are not only optimizing their internal operations but also setting new benchmarks for innovation, sustainability, and overall economic development. This transformative journey is reshaping not just how products are made but also how industries conceive of and interact with the physical and digital worlds, paving the way for a future where technology and human ingenuity coalesce to create a more efficient, sustainable, and prosperous society.