Application Highlight: How Premio Builds Industrial Computing One Block at a Time
April 29, 2024
Sponsored Story
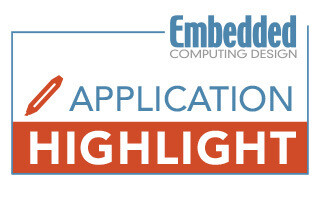
The Industrial computing space is getting more complicated all the time, and it can seem daunting when looking at the breadth of offerings and options available. A great place to start is with the “building block” approach.
When thinking about building blocks for industrial computing, it can be helpful to think about the key strategic applications that will make an industrial, supply chain, or manufacturing operation more efficient and effective, and what will be needed for those applications.
Automated Guided Vehicles (AGV) and Autonomous Mobile Robots (AMR) are taking the lead in guiding smart manufacturing in Industry 4.0 and are a great place to begin when planning embedded systems applications. Everything from supply chain efficiency and warehouse operations to factory floor and industrial plants can make good use of these automation tools to address critical challenges in logistics and operations.
In terms of building blocks, AGV and AMR deployments require rugged industrial computers for enabling edge AI applications in real-time, processing data from multiple IoT sensors and other inputs simultaneously, and powering hardware and connectivity technologies like 5G, GPU, and cameras. These advanced vehicular robotics need low latency to be effective, and processing edge AI workloads locally allow AGV and AMR to operate in real-time, minimize bandwidth utilization, enhance safety and security, and provide live telematics.
Application Use Case
There are almost unlimited applications and benefits for industrial computers, even limiting our scope to AGV and AMR.
Real-time processing might be the most asked-for capability in industrial settings. On warehouse floors or in an AGV itself, it’s important to have the power and memory for low-latency computing and decision-making. Performing compute functions in the cloud has been the traditional approach for a long time, but the challenges of latency, dependency on consistent wireless connectivity, and bandwidth constraints make it less desirable in a modern Industry 4.0 facility. Of course, AGV and AMR applications require low latency and real-time processing to effectively leverage AI decision-making.
Industrial edge computers managing real-time edge AI processing are deployed in the facilities and onboard fleet vehicles, so the processing doesn’t need to be sent to the cloud. A heterogeneous computing approach can enable sensor fusion, another key strategy, and specialized computing hardware accelerators allow engineers to consolidate IoT sensors, process and analyze edge AI workloads, and store data for further analysis. This means that 24/7 operational uptimes and optimal efficiency are both possible and obtainable thanks to embedded computing at the edge.
Almost as important is the longevity and reliability of the system. Industrial operators cannot afford downtime, and demand long lifecycles, even in cutting-edge robotics. Embedded industrial computers are designed to withstand harsh conditions and environments and should integrate components that follow embedded roadmaps for extensive product support for security and upgrades.
What’s more, when these industrial computers are deployed into critical AGV and AMR applications, reliability and safety are mission critical. Edge computing manufacturers must acknowledge and build for consistent reliability. This means using testing and validation from nationally recognized third-party laboratories and certification bodies.
Other factors like consistent and reliable connectivity and scalable and ruggedized designs are also necessary and will be included from reliable partners and suppliers.
Premio AGV & AMR Solutions
Premio offers several series of industrial computers full of key building blocks well suited for AGV and AMR, in addition to many other industrial applications. The RCO Series of X86 Super Rugged Computers, JCO Series NVIDIA Jetson AI Edge Computers, and ACO series in-vehicle computers each offer the elements needed to drive processing and intelligence to the edge.
Premio engineers have integrated the company’s embedded-centric hardware and software into their industrial computing solutions, offering prolonged support and reliability for up to 15 years. AGV and AMR integrators strategically partner with Premio to access the company’s lifecycle support and expertise on the latest computing architectures. The balance of performance and power efficiency that experts like Premio’s can provide will avoid deployment revisions due to end-of-life product updates and prevent mission-critical downtime and delays at any point.
In terms of ruggedization for industrial environments, Premio computers follow a fanless and cableless design. Fans are a common failure point and are susceptible to single-failure point vulnerability, so Premio’s engineers use passive cooling and keep the chassis fully enclosed, supporting a wide operating temperature range, resistance against shock and vibration, and wide power input range. Premio leverages modular EDGEBoost I/O technology to provide seamless configurability to meet high-specification deployment criteria and allows for additional LAN or USB, PoE support, and M.2 acceleration for 5G connectivity, enabling AI performance through TPUs, and NVMe storage.
Not all AGV and AMR deployments are the same, and each has its own processing performance, IoT connectivity, and other specific needs. Premio has a 3-tier performance selection for just this reason, ranging from entry-level building blocks to high-performance certified systems. Its EDGEBoost I/O modules provide connection flexibility for all kinds of deployment requirements with M12 connection, PoE support, 5G wireless connectivity, and M.2 performance acceleration.
For connectivity, both on-premises and to the cloud, if needed, Premio industrial computers provide whatever is needed to consolidate various AGV/AMR sensors, cameras, and
devices. They include support for both modern and legacy connectors to ensure compatibility across prevalent IoT sensors, cameras, and devices, in addition to automation and robotic I/O such as DIO for programmable switches, CAN Bus for real-time vehicle telematics, and an OOB (out-of-band) module for remote management.
Finally, Premio’s UL-Listed certification verifies that the product has undergone thorough inspections and has met all stated product claims for safety; allowing end users to quickly assess its compliance with safety standards for deployment confidence and peace of mind in their AGV and AMR system builds.
If you get the right tools and “blocks” ready, and get the help of the right partner, you can build the Industrial computing solution that will move your operation to the next level.
Additional Resources:
- Key Applications: https://premioinc.com/pages/agv-and-amr-robotics-powered-by-industrial-computers
- Product Page: https://premioinc.com/blogs/blog/how-to-choose-the-right-industrial-computer-for-agv-and-amrs