Preventative Maintenance for Automation: Break Machinery to Make it Better
June 24, 2021
Story
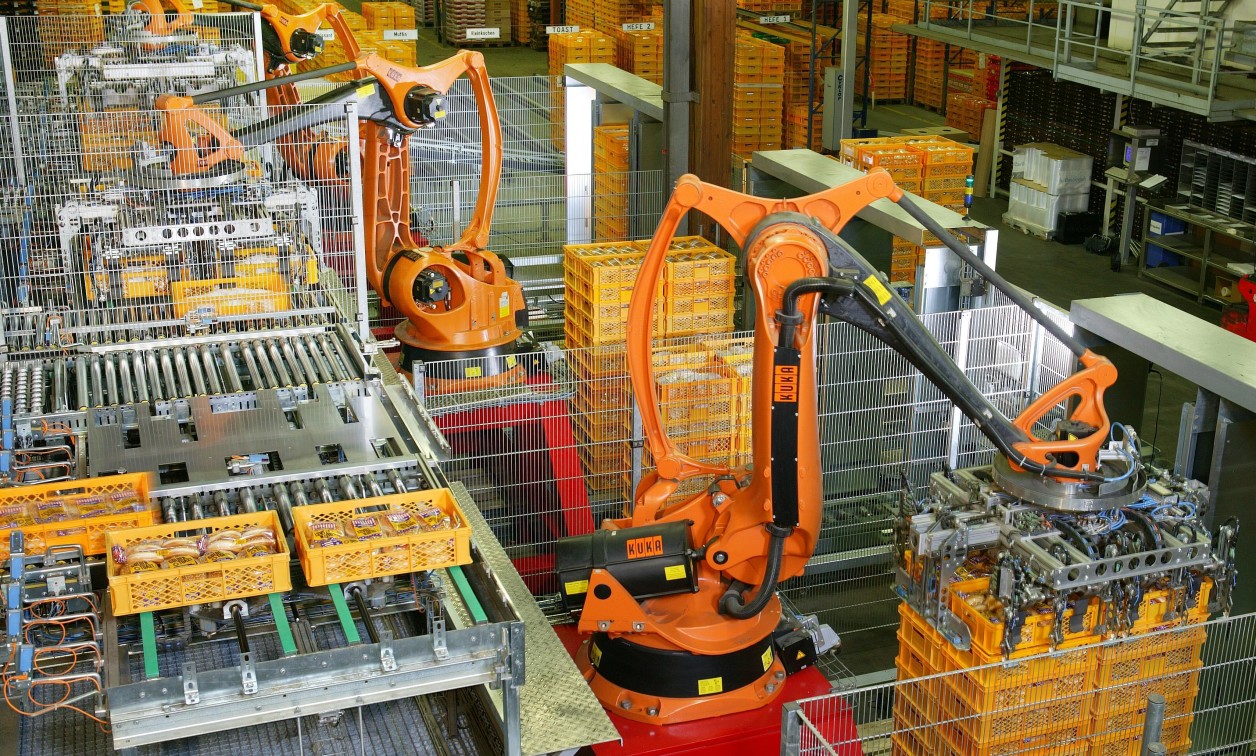
I now primarily work as a sort of tech journalist–documenting interesting projects and technology, while building a variety of projects that I can write about and sometimes sell. Before that, I spent well over a decade as an engineer working in manufacturing automation. In this arena, as in life, the universe, and everything, there comes a point where a “thing” works more or less as it did yesterday, but in a state that could be improved.
To make these improvements means that you must take a working process down to make changes as a part of preventive maintenance (in a “PM event,” or just “PM”) with no guarantee beyond your own skills, and that of those around you, that you’ll be able to make said improvements and revive the machine. Even worse, there is no “undo” button to set things back to an original state. In the case of a process that normally spits out tens of thousands of dollars in widgets per hour, if planned downtime goes longer than scheduled, management may get… antsy.
The alternative of course is for machinery to “plan” its own downtime by simply breaking down. This is inconvenient for everyone, as the company wants its products immediately, you may not have the proper parts available… and it usually happens right before lunchtime, or 30 minutes before you go home!
Putting the “Patient” Under
In my last job as a manufacturing engineer, I oversaw preventive maintenance events on two high-volume assembly lines. Such events normally took multiple days and were initially quite stressful. However, after doing a few PMs, I got better and more confident at orchestrating the process. If you are tasked with such a job, here are a few tips to help you on your journey. These concepts should also be applicable for a wide range of related scenarios:
- Make a Specific Plan: During these events I had a large spreadsheet with tasks that needed to be done and color-coded according to priority. Someone’s name was assigned to each, along with an estimated time of completion. Workers could put a line through each when done so we could track progress throughout the day.
- Specific Leadership: While I was normally an individual contributor, during this time I was in charge of telling many people what to do. While difficult at first, I eventually came to enjoy the challenge. Do not be afraid to embrace this role when called upon. On a related note, while there is nothing wrong with getting your hands dirty at times, it’s often best to have someone else do the job so you can survey the overall situation.
- Personnel: Extra personnel were brought in during these events, and shifts were extended. “Throwing people at the problem” works, but it had to be organized. As noted earlier, specific written directives were especially helpful when the off shift was working by itself.
- Parts Available and Staged: As the engineer in charge, along with my spreadsheet, I packed up several boxes of tooling and spare parts that I knew would be needed. I then parked them next to the machine. If this was not finished, technicians would have to travel, and search for parts, while wasting a huge amount of time during the day.
- Maintenance and Improvements: Parts that wear out, and other items that must be lubricated, cleaned, and otherwise maintained. There are also things that you would like to upgrade, measure, or improve, and machine downtime presents an opportunity for this as well. Both are good, but as time ticks down, priority ultimately must be given to getting the machine up and running again.
- Adjust Plan: No plan survives contact with the enemy, or so the saying goes, and as a PM event unfolds, things may take more or less time than you anticipated. It is important to monitor your specific, yes I am purposely repeating the word plan, to see if you’re running behind according to it. You can then make adjustments and cut non-critical items to meet the schedule.
- Backup: If you make programatic changes, save your starting point, and organize each of these ways in a methodical way (e.g. dated file names). Organization makes it easier for you to go back to a previous state, or for other engineers to do so if you’re not around. There may be better ways to organize code than what we used, but the important thing is to do this, and be consistent with organization.
- Record: Sadly, I do not have any images of how these PMs went, and actually very few of my work in there general. Take a few pictures, perhaps even a time-lapse of your progress. Your future self will probably appreciate it.
After Successful Mechanical Surgery
- Debrief: What went right? What went wrong? What can you check off your spreadsheet, and what needs to be carried over? Preparation for the next planned downtime starts as soon as the one you just accomplished ends, and you might even call a meeting with parties involved to debrief.
- Improve PM Tools: Sometimes certain PM operations take a long time, but they do not necessarily have to. One big improvement can be buying or making spares of subassemblies that can be quickly swapped out, rather than servicing them while the PM is going on. This was a massive improvement for these operations. Most notably, our machine shop made quite a bit of spare tooling, and I purchased bearing blocks that could be changed out instead of rebuilding them, saving hours on machine-down labor.
- Analyze: Make your best effort to record how a machine is running before and afterwards. This will help you convince supervisors that, yes, all that logged downtime was worth it. While I never did, thinking back on it I wish I had recorded how long PMs took to see if we were getting faster. While I am sure things did become faster, just how much faster is an open question.
[Caption: After maintenance, you can finally relax, have that donut... and perhaps even clean your office.]
With maintenance done, more than likely one’s job as a manufacturing engineer will become easier for the immediate future, production will hopefully have a machine that runs significantly better than before. You can then relax just a bit until the next event where you need to again take control of the situation until the purposely broken machine is reborn.
While my experience is in industrial automation, there are certainly parallels in the variety of pursuits. One’s bathroom probably worked OK before a stressful renovation, a car’s tires nominally worked before replacement, and Windows 95 and Netscape Navigator were fine for their time. Things need to be upgraded and maintained to stay current, but the upgrade process can be difficult. Prepare as you can, then jump. You will feel better afterwards!
Jeremy Cook is a freelance tech journalist and engineering consultant with over 10 years of factory automation experience. An avid maker and experimenter, you can follow him on Twitter, or see his electromechanical exploits on the Jeremy Cook YouTube Channel!