Embedded Workstations Drive Intelligent Autonomous Forklifts
December 04, 2024
Sponsored Blog
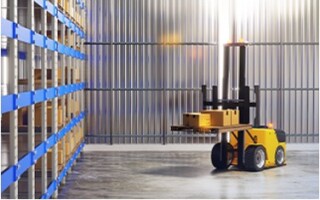
Forklifts, or motorized lifting trucks, have been around for about 100 years, first appearing around World War I. In the 1950s and 1960s, forklift technology advanced rapidly as the post-war economic boom drove demand for efficient material handling. Hydraulic lifting mechanisms became standard, increasing lifting capacity and precision. Safety features were added, addressing the risks associated with higher lifting and heavier loads.
The 1980s and 1990s saw the rise of electric forklifts, with improvements in battery technology allowing for quieter, emission-free indoor operation. This shift catered to stricter environmental regulations and the growing need for clean operations in warehouses.
Today’s forklifts are more powerful and efficient and are increasingly becoming part of a connected ecosystem, reflecting advancements in automation, sustainability, and safety. The latest models are designed with many state-of-the-art technologies, including lithium-ion batteries, advanced safety sensors, and automated guided vehicle systems. The latter feature puts the forklifts into the same category as an autonomous mobile robot (AMR).
The results of these technologies include longer runtimes and faster charging, while the automated forklifts can operate autonomously, navigating warehouses without human intervention. Additionally, data analytics and connectivity enable fleet management and predictive maintenance, maximizing efficiency and uptime. Some of the applications that have learned to maximize the automated forklifts include retail, construction, forging and casting, food storage, manufacturing, lumber, paper, and recycling products, and intermodal shipping/ports.
Autonomous forklifts are becoming more common in today’s workplace. If implemented properly, they can handle repetitive tasks very efficiently.
This evolution has transformed forklifts into critical components of modern logistics and supply chains. At the same time, the forklift market is growing, driven by e-commerce expansion, automation, and warehouse optimization demands. Electric models, particularly autonomous forklifts, are becoming quite popular, as companies look to streamline operations, reduce labor costs, and enhance safety in logistics and supply chains.
The industry is looking to double down on these technologies, especially as we are seeing further labor shortages, specifically referring to the number of on-site operators, such as forklift drivers or warehouse workers. Many companies are also seeing rising labor costs and a higher worker turnover combined with difficulties in recruiting and retaining warehouse workers. This could be the result of the repetitive and physically demanding nature of work involved in this field, which is becoming less interesting to the younger workforce. When you add all these components together, automated equipment, such as unmanned forklifts, represent an effective solution.
Financial Impact of Autonomous Forklifts
Autonomous forklifts can significantly reduce labor costs by minimizing the need for human operators, especially in 24/7 warehouse operations. They improve efficiency, reducing downtime and optimizing workflow with precise, consistent performance. Maintenance costs are also lower due to predictive technology and reduced human error, which can prevent accidents and repairs. Though the upfront investment can be higher, the long-term savings and operational efficiency typically contribute to a favorable return on investment (ROI). Today, automated forklifts are quite common in parts of Asia, specifically in Japan and Korea, with demand expected to grow in both the U.S. and Europe.
Users of autonomous forklifts expect seamless integration with existing warehouse systems and precise navigation to prevent accidents and reduce product damage. Users also expect adaptability to various tasks, from transporting pallets to stacking items at different heights. In addition, ease of use, intuitive controls, and real-time monitoring capabilities are highly desired, as they ensure that these forklifts contribute effectively to productivity and overall warehouse optimization.
Dissecting the Automated Forklift
The robotics subsystems within the automated forklifts rely on advanced sensors, cameras, and lidar systems to map, navigate, and adapt to dynamic environments. Processing power is critical, as onboard microprocessors quickly interpret data from the sensors, detecting obstacles and adjusting routes in real-time. High-level algorithms enable object recognition, spatial awareness, and predictive motion planning, allowing autonomous forklifts to safely and accurately make split-second decisions.
Connectivity is essential for coordinating multiple robots and integrating with a warehouse’s current management system. Generally through Wi-Fi or 5G cellular networks, forklifts communicate with a central system, sharing their location and task status in real-time. This connectivity enables route optimization, traffic management, and task assignment based on priority, ensuring safe, efficient, and coordinated operations across the fleet. Additionally, cloud connectivity allows data collection and analytics, improving predictive maintenance, load tracking, and workflow optimization.
Powered by the latest Intel Core i9/i7/i5/i3 processor, the Vecow embedded computer is highly suited for autonomous forklift applications.
The Vecow ECX-3200/3100 Embedded Workstation
The Vecow ECX-3200/3100 expandable fanless embedded workstation is highly suited for use in automated forklifts, as it offers the robust processing power, connectivity, and durability that is essential for autonomous operations. Powered by the latest Intel® Core™ i9/i7/i5/i3 processor (14th gen, RPL-S refresh), the platform provides the high-performance computing needed to process large volumes of data from an array of cameras and sensors in real-time, enabling rapid decision-making and precise navigation.
This workstation’s fanless design ensures reliability in dusty, high-vibration warehouse environments, minimizing maintenance and downtime—a crucial factor for consistent forklift operation. Its wide operating temperature range (-40°C to +75°C) further enhances durability, allowing it to withstand varied warehouse conditions.
Thanks to embedded computers like the Vecow ECX-3200/3100, autonomous forklifts can reduce labor costs, improve efficiency, and optimize workflow.
The high-performance, workstation-grade computer is designed with Intel’s R680E PCH platform, meaning that it can accommodate up to 24 Intel Core i9 CPUs running with the R680E PCH. In addition, it supports remote and smart management features, Intel’s vPro, TCC, TSN, TPM 2.0, and multiple SIM sockets for seamless wireless connection. Together, these are key features for fleet-management applications. It can be configured with PCIe x16 expansion with a maximum power budget of 200 W, which is needed for multi-axis motion control cards for servo or stepper motor control.
Additional connectivity options, including 5G, Wi-Fi 6, and dual LAN ports, suit the ECX-3200/3100 for real-time communications with central systems, supporting continuous updates on location and task status. This connectivity enables integration with warehouse infrastructure. The workstation’s expandability allows for customization for specific warehouse needs, such as adding extra storage or specialized interfaces. It also helps accommodate future needs and upgrades.
For more information about the Vecow ECX-3200/3100 expandable fanless embedded workstation, or anything related to automated forklift technology, contact Vecow today. The company’s experts operate on all continents and can serve all your embedded computing needs.