Powering the Next Generation of Connected-Health Wearables and Hearables with Solid-State Lithium Microbatteries
August 12, 2022
Blog
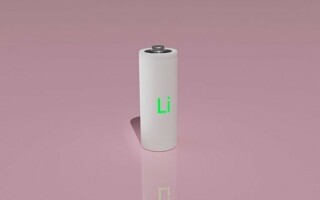
As solid-state lithium battery technology grows in adoption — especially for electrical vehicles (EVs) — it is equally attractive for an emerging class of 1 to 100 milliampere-hour (mAh) applications that need a combination of high energy density and small, customizable form factors. The latest solid-state lithium manufacturing and packaging advancements improve microbattery capacity and cycle life without sacrificing performance or energy density and create extensive new options for customizing microbattery shapes and sizes.
As an example, the availability of solid-state lithium (Li) microbatteries that are manufactured using proven anode-less chemistry and more scalable production and assembly techniques than prior battery technologies will enable connected-health product developers to add features and lengthen the time between charges. It will also allow developers to create more capable and comfortable health-tracking rings and even clothing as well as multifunction “hearables” that need wireless connectivity and a more comfortable fit in the ear canals as recently passed legislation moves them closer to broader, over-the-counter (OTC) availability for hearing assistance.
As solid-state lithium microbatteries grow in adoption, developers will harness the power of two main advancements: higher Volumetric Energy Density (VED) and form factor freedom.
Increasing VED
When evaluating battery technologies for wearables and hearables, the most important energy density metric is how much energy can be stored per unit volume, or VED. The higher a battery’s VED, the more energy it can store for its size. Calculated by dividing energy by volume, VED is measured as Watt-hour per liter (Wh/L). If two batteries have the same capacity and one is twice the size, then the smaller one has twice the VED.
VED plays a critical role in determining how small, say, a hearing aid can be, whether it can be shaped to fit comfortably in the ear canal, and whether it can incorporate the necessary features that optimize sound amplification and fidelity, among other hearing-assistance functions. It also needs to last as long as possible before a recharge.
VED is also important for digital health and sports/fitness wearables. As an example, health-tracking rings now monitor sleep, heart rate, heart rate variability, respiration, temperature, blood oxygen, steps, and calories – with additional features like glucose and blood pressure monitoring on the horizon. Powering the wireless connectivity for these applications requires batteries that are small and deliver the highest VED possible.
Over the past two decades, Li-ion coin-cell microbatteries have been the predominant option for these devices. The electrolyte used in Lithium-Ion (Li-ion) batteries is vulnerable to ambient air as it seeps into them and causes damage so manufacturers must include safety mechanisms and packaging that, because they take up space, further reduce the VED. These Li-ion batteries also need thick interior walls and partitions to protect them, making it difficult to power a new generation of wearables products that need even higher VED for new features and/or longer charge times.
Solid-state lithium microbatteries solve these problems by offering several improvements over conventional Li-ion batteries. First, they enable a new architecture that does not require the liquid electrolyte of Li-Ion coin-cell products. An inherently safe solid electrolyte is used instead. In addition, a thin stainless steel substrate can be used to improve VED while also providing greater mechanical strength, reducing microbattery volume and serving as both a conductor and hermetic moisture barrier. Second, this architecture facilitates the use of ultra-compact, semiconductor-style stacking and packaging of the energy-producing cells within the battery, further improving VED.
Early testing of solid-state lithium microbatteries against traditional coin-cell options shows an improvement of up to twice the VED, along with up to triple the charge cycles, more than twice the charging speed (Figure 1), and more than ten times the high-pulse discharge speed. These capabilities will improve the user experience for products like hearables that will need more processing power and longer periods of more frequent wireless connectivity without increasing the size of the device.
Figure 1. Solid-state lithium microbatteries offer multiple performance advantages over their Li-ion predecessors.
In addition to boosting VED and other microbattery performance metrics, a solid-state lithium architecture also releases designers from the form-factor constraints of previous technologies.
Unleashing Form-Factor Innovation
Batteries have traditionally been cylindrical because that form factor was easier to build. It also was a safer packaging choice for batteries containing a liquid electrolyte. Some prismatic and rectangular pouch battery options exist for larger capacity devices such as smart watches and smartphones, but connected-health hearables and wearables have been stuck for the most part with a cylindrical coin-cell Li-ion rechargeable battery. Worse, there were only a small number of standard size options unless high product volumes justified these customized sizes.
Solid-state lithium microbatteries change these dynamics by enabling customizable, rectangular form factors, using proven high-volume, roll-to-roll manufacturing techniques. These techniques are used to deposit the microbattery’s cathode and solid electrolyte. Next, the unit cells are cut from the roll at customized lengths and widths. A customizable number of these cells can then be stacked to the desired height based on the required capacity (Figure 2).
Figure 2. Cell stacking maximizes VED and enables customizable form factors and support for direct Printed Circuit Board (PCB) connection on both sides. Combined with the solid electrolyte’s ability to withstand high temperatures, this method simplifies end-product assembly compared to earlier coin-cell techniques.
In addition to facilitating customization for specific capacity and design requirements, solid-state lithium microbatteries are more robust and reliable than their coin-cell counterparts. Encapsulating and metallizing the stacked cells enables connectors to be added on both sides for direct PCB connection. Figure 3 shows the typical manufacturing flow of a solid-state lithium microbattery. Since these microbatteries can withstand higher temperatures, standard Surface Mount Technology (SMT) can be used to assemble the microbatteries onto PCBs with a lower temperature (up to +160°C) reflow profile.
Figure 3. A solid-state lithium microbattery architecture enables cell stacking using proven and scalable roll-to-roll techniques, plus multi-layer die stacking augmented with encapsulation and metallization for a robust and reliable 1 mAh to 100 mAh microbattery.
Solid-state lithium microbattery architectures are critical for realizing the full potential of, say, a slim and stylish fitness ring that, ideally, should deliver continuous updates from multiple sensor inputs and work all day without recharging. The same architecture will also enable hearables with more processing and connectivity features that look much more like non-stigmatizing consumer earbuds. As they enter the market, these and other connected health and fitness products will be transformed by new, higher-performance, high-energy-density microbatteries that can be manufactured in customizable form factors with greater precision, efficiency, and scalability than was previously possible.