You want to play with lasers? Take safety seriously
January 06, 2017
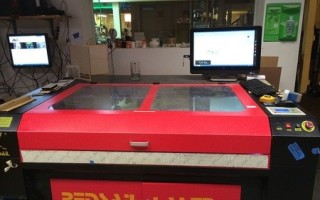
If you grew up in the 1980s (or likely earlier) and were interested in technology whatsoever, you probably thought lasers were pretty awesome. Portray...
If you grew up in the 1980s (or likely earlier) and were interested in technology whatsoever, you probably thought lasers were pretty awesome. Portrayed in science fiction as amazing handheld weapons, or in actual scientific documentation as devices for advanced experimentation, getting your hands on one once seemed like a far distant fantasy.
This fantasy is now a reality, and cheap laser pointers can be had for a few bucks. Those capable of actually cutting something are a bit more, but can be had for a few hundred dollars. Entire cutting systems, including a gantry to maneuver the laser can be had for under $1000 for the cheapest models, though may take some effort to get working.
On the other hand, you still need to observe appropriate safety precautions while using them. Although I’m relatively new to using laser cutters, as I see it there are two major safety concerns that aren’t always present in “traditional” manufacturing methods.
Unconstrained light
If you’re used to working with tools such as a CNC router, you know that unless there is some extraordinary circumstance, a clear physical barrier between you and the part protects you from debris. Lasers, however, aren’t necessarily constrained by a transparent barrier and can be dangerous, especially to your eyes, even if you can’t physically come into contact with it.
This can be mitigated by surrounding your laser with a protective covering, and/or laser safety glasses. Note that all glasses are not created equal. In fact, even high-quality glasses might not be appropriate for your particular laser, as these glasses block light in certain wavelengths and not others. Since the wavelength emitted varies depending on your laser type, make sure to match this up correctly. The other thing to consider with safety equipment is the optical density (OD).
The higher this number, the more light is absorbed. Be sure you get the appropriate safety gear for your application. Many ready-built laser cutters come with a protective covering, but you’ll have to take care of this yourself if you build your own. Along with a protective box, I used this shielding panel from J Tech photonics. It appears to work well, and is quality checked via the ANZI Z136.7 specification/methodology, according to the company.
Fumes
Unlike most machining processes, you’re actually burning, not cutting, the material that you’re working with. It’s critical that you have some sort of fume collection to keep most of the dirty air out of your workspace.
Beyond just removing most of the fumes, there are some materials that emit truly noxious and possibly deadly gasses when burned. You can see a list of some of the terrifying possibilities on the ATX Hackserspace page, a version of which also appears on the Tampa Hackerspace Laser Wiki. Nasty possibilities vary from chlorine and cyanide gas in the air to materials catching fire and/or melting in the equipment. So, seriously, give some thought to the materials you’re using!
[Tampa Hackerspace member David Redding made these models using their laser cutter.]
Good news
The good news is that there is a long list of materials that do cut well. Given the right conditions, a properly-used laser cutter can produce good samples or even low-volume production runs. There are lots of possibilities for MakerPro endeavors using these devices, but you should seriously consider your (and others’) safety before using one.