Custom design HMI front ends for electronic equipment
August 09, 2016
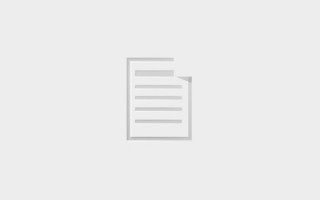
Interactive electronic devices require a human-machine interface (HMI) that allows a user to communicate with the underlying electronic device. That r...
Interactive electronic devices require a human-machine interface (HMI) that allows a user to communicate with the underlying electronic device. That requirement can be satisfied using an embedded computer with touchscreen/display attached to a larger device that enables user interaction. But how can such an HMI front end be implemented for specialized industrial, medical, and military applications?
In today’s embedded devices, the HMI fundamentally consists of four items including the display, touchscreen, processor, and operating system.
Display
The display provides visual communication of the machine’s status and application data to the user, and requests input from the user. Flat panel displays, including LCDs and OLEDs, are the hardware mechanisms that implement the display. Critical technical attributes for displays include not only size and resolution, but also brightness, viewing angle, special use cases for readability such as bright environments including direct sunlight, and operational temperature range that may include extreme levels of heat or cold.
Touchscreen
The use of touchscreens for information input on complex machinery is growing. The two major touchscreen technologies in use today are capacitive and resistive. Projected capacitive technology is used in most smart phones, but may not be the best choice in wet or noisy electromagnetic environments, or with the use of thick gloves. Resistive technology has been used for many years in these environments, but is more easily scratched and is less optically clear than capacitive. Critical parameters include the required touch resolution, use of a stylus or other touch instrument, number of simultaneous touch points, gesturing, environmental conditions, and impact resistance.
Processor
A processor typically controls the HMI subsystem, rendering images and driving them to the display, accepting and interpreting touch input, and processing instructions for the system. For low resolution and/or static images with limited processing needs, a microcontroller, perhaps running a real time operating system (RTOS), can be utilized. For high resolution displays, motion video, or complex systems, a microprocessor which can run a complex operating system may be required. Processors with hardware-accelerated video and graphics engines offer optimal power/performance tradeoffs. The processor may respond to user input within the HMI subsystem or communicate instructions and/or data beyond the HMI via interfaces like RS-232, UART, Wi-Fi, PAN, Ethernet, or USB.
Operating System
The operating system is software running on the processor, which simplifies application development by providing a means of communicating with peripherals such as the touchscreen, display, and other interfaces. When optimized for a specific circuit board, the operating system is called a board support package (BSP). HMI devices typically implement Android, Linux, or Windows operating systems. Android greatly simplifies software design for user interaction in HMI devices.
HMI for embedded applications: a highly complex subsystem
The combination of these four elements into a functional HMI subsystem involves a great deal of complexity, both for technical and business reasons.
Circuit board design
Circuit board design for modern microprocessors is complex. With multiple hundreds of processor package connections and associated circuit board traces to memories, power supply components, and a variety of peripherals, there is ample opportunity for schematic mistakes and routing signal integrity problems. The occurrence of these problems can lead to long debug cycles, expensive respins, and associated schedule slippages. Such design is often best outsourced to a knowledgeable company who understands embedded microprocessor operation and regularly delivers these designs.
Display/touchscreen
The touchscreen interacts with the underlying display optically, mechanically, and sometimes electrically. It is therefore important to treat the display and its touchscreen as a subsystem, with both being optimized for the HMI application. Together, the display/touchscreen is mounted in a package that meets ruggedization requirements and aesthetics. Availability of appropriate display and touchscreen components is often a factor. An experienced HMI designer can help facilitate the various performance, cost, and availability tradeoffs.
BSP customization
The BSP usually requires customization to the embedded processor platform on which it runs. Drivers for special peripherals may require development. Removal of functions not implemented may prevent crashes. For embedded HMI systems, a custom splash screen and booting directly into a fixed application (often called kiosk mode) may be necessary. Enhanced security may be desired. Developers who customize the BSP must not only understand the operating system itself, but also the intricacies of the underlying hardware as well as how application developers expect to interact with the BSP.
Environmental
Being accessible for human use, HMI front ends are often uniquely exposed to harsh environmental conditions. The touchscreen/display, often made of glass, are susceptible to impact which can crack or shatter the device. Scratches can impact viewability. Moisture can seep around front bezels and into internal circuitry. Glare from bright lights or the sun can render a display unreadable. Wide temperature ranges, for devices used outdoors, can cause operational problems, often in corner cases. Fortunately, proper system design that accounts for electronic, mechanical, thermal, and optical design can assure a robust product.
Regulatory certification
All electronic products, regardless of industry, application, or use case, must minimally pass regulatory certification. In the US, at a minimum, FCC Part 15 testing for EMI/EMC is required. Other countries have similar requirements like CE certification in Europe and IC certification in Canada, for example. While an HMI front end is typically certified with the machine to which it is attached, its designer must be familiar with design for electromagnetic compliance to enable the certification process to go smoothly. Having an experienced business partner with a history of designing HMI interface devices and moving them through the certification process can be critical to a successful product launch.
Product life cycle
Product life for industrial, medical, and military devices far exceeds that of consumer products, including sale and support, often by a decade or more. Availability is a function of the components selected and subsequent monitoring for obsolescence. Most critically the processor, display (with touchscreen), and other vital components must be selected with life span factored in. Consumer-oriented processors, displays, and complex peripherals like wireless modules are usually available for no more than 2-3 years. It is critical to understand the supply chain during the design phase.
Customized HMI design
Given this wide range of design parameters, a complex machine often requires a customized HMI, typically to meet display, touchscreen, and peripheral requirements. The underlying processor circuitry can usually be leveraged with minor modifications for the specific display, touchscreen, and peripherals. When looking for a custom HMI, look for a solution that starts from a known, proven design to reduce development time, cost, and risk.