More Useful 3D Printed Parts
December 30, 2021
Blog
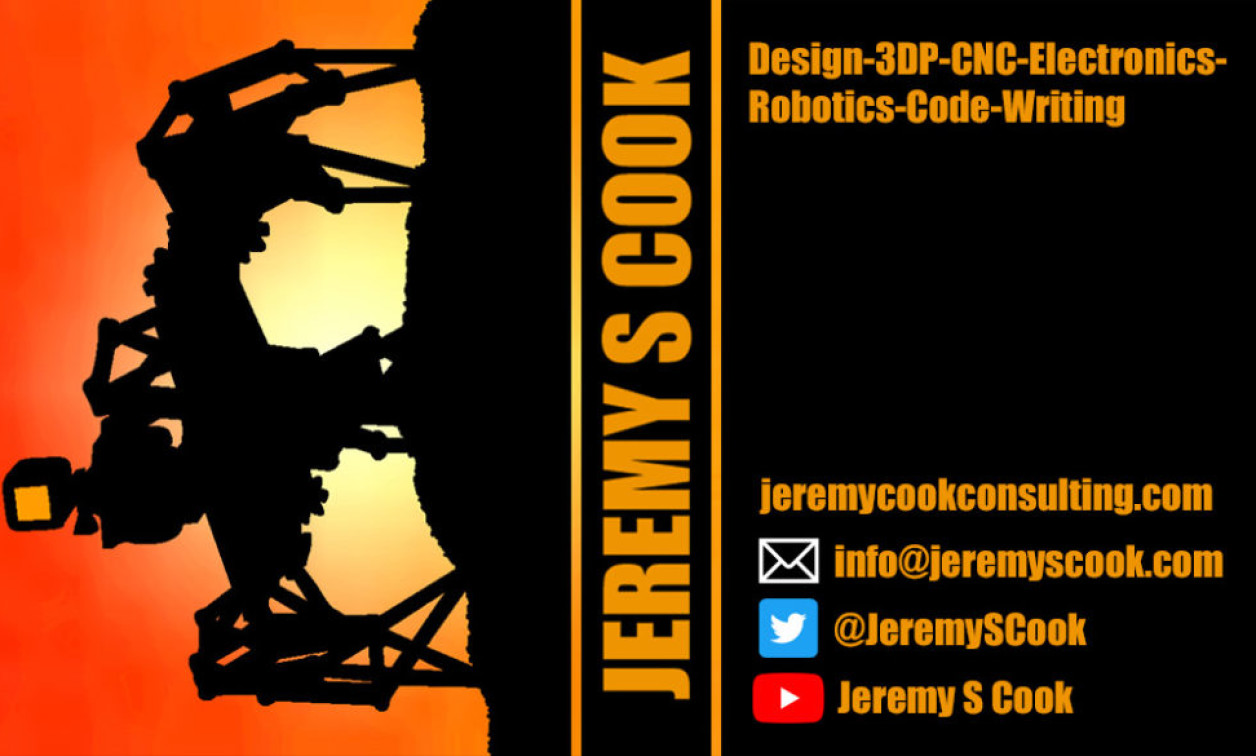
Nearly 2 years ago, I wrote an article about my favorite useful designs for 3D-printing. As it just so happens, I recently put out a time-lapse video of my last 2 years of 3D-printing. While there were a few decorative items thrown in, the vast majority of my printing efforts involved useful implements, so I think it’s time for an update!
Refined Design: Headphones Hanger
In the post mentioned above, there’s a 3D-printed headphones hangar pictured that I was quite proud of. It uses a screw to apply pressure and hold it in place, which, if memory serves me correctly, eventually broke. Even when working correctly, removal was inconvenient.
Caption: Ridge on top nearly invisible, but effective
Image Credit: Jeremy Cook
Rather than let my headphones languish on the floor or take up desk space, I redesigned it as a snap-on fixture using neodymium magnets to secure it in place. This worked, but after knocking it off the stand repeatedly, I redesigned it yet again to incorporate not just magnets, but small ridge on the top to fixture it mechanically. Between these two complimentary fixturing methods, I’ve yet to knock it off unintentionally, though it can be removed easily when needed.
I use it on a daily basis, and it’s illustrative of how 3D printing, along with modeling skills, can allow you to easily change a design until it fits your needs perfectly. As with other 3D-printed implements that I have around my house, it’s not dramatically life-changing, but makes things slightly better.
Laser Fume Extraction and Accessories
As outlined here, in late 2020 I purchased a laser cutter. This has been a great tool, enabling a wide variety of projects. Ironically enough, setting it up involved using a number of 3D-printed parts for fume extraction, a mount for a nearby Ethernet switch, and a tool to help remove one of the laser’s mirrors for cleaning.
Jigs
Caption: Key switch jig, new improved version being sliced
Image Credit: Jeremy Cook, screencap
I was once told that you should spend about 50% of your project time building jigs–i.e. custom tools to make other things. Whether or not the number itself is true, they’re definitely worth the effort in many cases. I’ve made several jigs for proper key switch assembly on my JC Pro Macro and JC Pro Macro 2 (JCPM2) keyboards. These have been useful on the original boards, and should be essential when fulfillment starts in earnest on the JCPM2. Additionally, I made a jig to solder up the PCB light cubes shown here, which I plan to eventually use in a video.
Interesting how 3D printer sits idle for days/weeks, then ideas/projects come to mind and it's super active for a while. Jig for #JCPM 2 switch alignment. Hopefully the thin walls aren't a problem: pic.twitter.com/XLrtbIrWY1
— Jeremy Cook ? (@JeremySCook) November 4, 2021
Of course, jigs aren’t always the optimum solution. Making a jig to line up the holes on my bunk bed build was likely unnecessary, and could have been accomplished at least as effectively with a tape measure or square. Still, perhaps it added something to the video and made it a bit more tech-centric.
Inexpensive and Adaptable Parts
The macro keyboards mentioned above feature a beautiful rotary knob, as well as an clear laser-cut acrylic base as options. While these are, in my opinion, quite nice, they add a bit of expense to the project and are something of a one-size-fits all solution.
As an alternative, I've put up two 3D-printed base designs, one with an angle for enhanced ergonomics [print files]. As shown below, Pat Regan, an early prorotype tester, has even experimented with a parametric knob generator, which opens up all kids of possibilities:
I'm using 3 keys now. 7 controls my video lights. 8 switches between headphones/speakers. The knob is volume control unless Davinci Resolve is in focus.
— Pat Regan (@patsheadcom) September 22, 2021
When it is, the knob moves forward or back in the timeline. F11 toggles the knob between 1 frame or 1 second at a time. pic.twitter.com/fF7WbZgq1Q
Other Implements
Image Credit: Jeremy Cook
I was quite happy with how this cordless Ryobi drill holder turned out [print file], presenting it at-the-ready at all times. I even designed in a slight angle for easy access. In other drill related news, I printed out a guitar tuning peg adapter for the drill designed by someone else [print file], which should be quite helpful when taking strings off, though perhaps overly powerful when actually attaching strings.
Quick draw and batter change demo: pic.twitter.com/hU5M0ePj2d
— Jeremy Cook ? (@JeremySCook) June 2, 2021
So, while 3D printers are still known in some circles as sources for decorative items and small trinkets, for me it continues to be one of the most useful tools in my shop. Once you have one, you start seeing more and more applications where it could be put to use!
Jeremy Cook is a freelance tech journalist and engineering consultant with over 10 years of factory automation experience. An avid maker and experimenter, you can follow him on Twitter, or see his electromechanical exploits on the Jeremy Cook YouTube Channel!