Bringing Next-Generation USB Power Delivery to Vehicles
December 09, 2019
Story
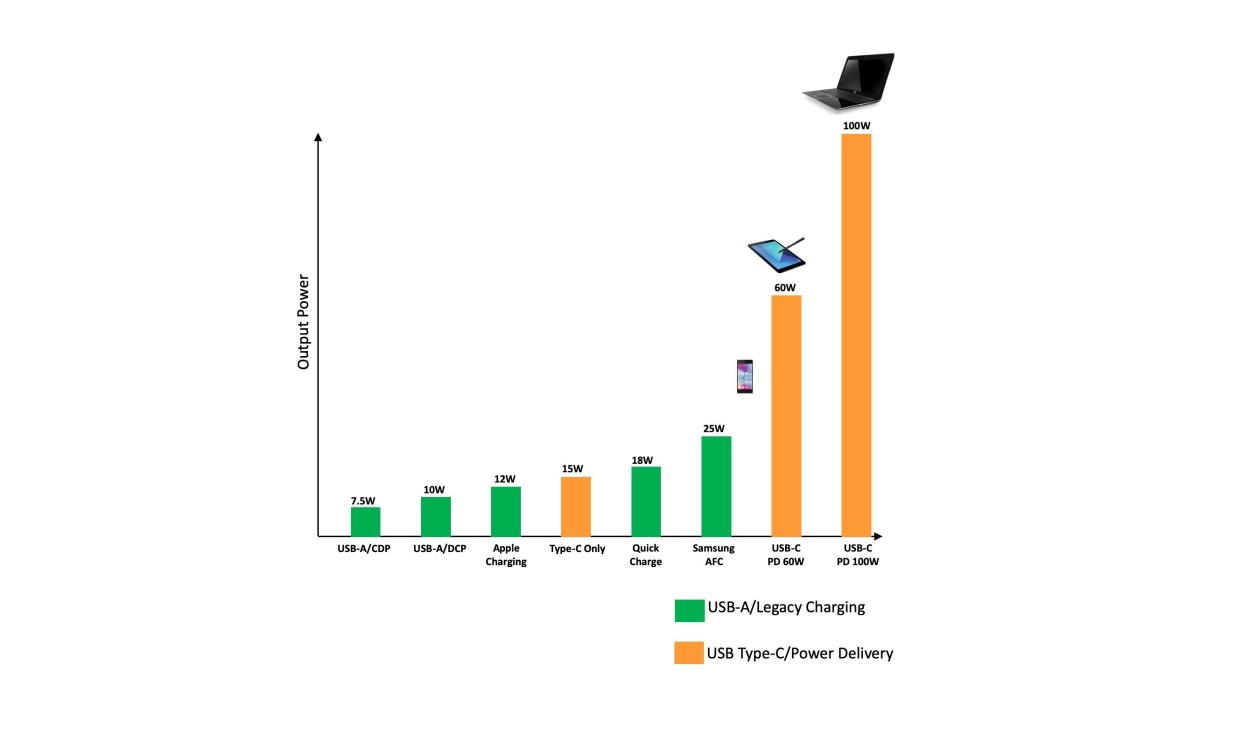
With the widespread adoption and use of portable electronics, it is becoming increasingly important for users to be able to charge their devices in their cars while they drive.
With the widespread adoption and use of portable electronics, it is becoming increasingly important for users to be able to charge their devices in their cars while they drive. The power delivery feature of USB makes device charging extremely convenient for users. In addition, USB’s high data rate enables next-generation infotainment systems to support a wide range of in-vehicle capabilities such as audio playback, screen and app sharing, data connectivity, and many others.
The traditional USB Type-A connector, already available in models from all major automotive OEMs, provides power capabilities up to 7.5 W (up to 1.5 A current at 5 V). However, with the rapid adoption of the USB Type-C connector in PCs, smart phones, and other portable electronic devices, USB Type-A is quickly becoming a legacy connector: The USB Type-C semiconductor market is projected to reach over 900M in 2022 (Source: Gartner 2018 and Cypress estimates).
The USB Type-C connector offers a more compact form factor than USB Type-A connectors with the additional advantages of universal connectivity, reversible plug orientation, and reversible cable direction. It also supports significantly higher power delivery, up to 100 W (up to 5 A at 20 V). The ability to provide substantially more power than 7.5 W enables compelling new usage models, including faster charging and the ability to simultaneously charge the increasing number of active devices in the car, including tablets, laptops, and even electric shavers.
However, implementing USB Type-C with next-generation power delivery in vehicles involves much more than just increasing the voltage and electric current to the port. It also requires a different approach to design than is typical for USB-based commodity- and consumer-level products. This article explores how USB will be used in vehicles, the required features in a USB Type-C and Power Delivery controller, interoperability implications, and key factors to consider when designing with USB Type-C.
The Importance of Power Delivery
The faster pace of our world means we need to be able to charge our devices faster and more often. With power delivery at 100 W, for example, it becomes possible for a salesperson to charge both a laptop and phone in the fifteen-minute drive between meetings. Similarly, parents can be confident that their phones – and the kids’ tablets – aren’t going to run out of power on a long trip.
Higher power delivery is key to in-car USB. Certainly, users could use a USB Type-C to Type-A adapter to charge their new phone using a legacy port. However, they won’t get the full benefits of USB Type-C. Rather, their next-generation phone, capable of fast charging, will be limited to the 7.5 W maximum delivered by USB Type-A. Clearly, the availability of full power delivery will play an important role in customer satisfaction and differentiating between vehicle models.
It’s unlikely that automotive OEMs will need to provide the full 100 W to each USB Type-C port in the vehicle. To reduce costs without significantly impacting charging time or reliability, a single 100 W supply can be shared between ports, known as dynamic load sharing. For example, intelligence in the USB Power Delivery controllers and the firmware can drop the power to one of the USB Type-C port to 60 W, so it can provide 40 W to the second port when a device is plugged in.
The USB Type-C and Power Delivery Controller
To handle the complexities of the USB Type-C and PD protocols, these controllers integrate an embedded microprocessor with PD controller logic. Typically, firmware for this microprocessor will be provided by the controller manufacturer, either as a downloadable file or generated by the development environment.
Achieving USB certification is just a minimum requirement if an OEM wants to provide a robust solution over the long operating life of a vehicle. The controller should also be supported by a mature software stack that has been proven in the field so that the USB subsystem is reliable. In addition, interoperability is essential. Just because two devices meet the USB specification doesn’t necessarily mean they will work together.
Interoperability plays a key role in automotive applications as poor interoperability can have a negative impact on user satisfaction. The USB port has grown to become a high-profile function of a car, bearing increasing responsibility for charging, steaming music and interacting with smart phones. When purchasing a vehicle, people will often be more aware of how easily they can connect their phone and play music than they will be of how well the engine runs.
Because of their extended operating life, vehicles need to be able to interoperate not just with nearly every smartphone, tablet, and laptop available today but with those to be released over the next few years. Interoperability is even more important when you consider that the typical smart phone is replaced every two years.
In addition, the USB power delivery standard may evolve over time, as many standards do. For example, the current standard supports Power Delivery (PD) 3.0 with programmable power supply (PPS) support and Quick Charge (QC) 4.0. If any of these specifications change – in fact, both the USB Type-C and PD specifications have been continuously changing – the vehicle may not be able to fully support new devices that are brought to market.
The only way to achieve robust interoperability is through a programmable USB controller. With a programmable controller, it is possible to upgrade the USB Power Delivery stack to interoperate with new devices. With so many parts of a car using software, drivers are coming to accept that software upgrades are a standard practice. Often these upgrades are transparent to car owners since it is common practice for technicians to begin with a firmware upgrade when a vehicle is brought in for servicing.
The fact that a controller has an embedded microprocessor does not necessarily mean that it supports programmability. A fixed-function USB controller, for example, does not need to be programmed and may be available at a lower cost. Alternatively, a configurable controller can be used that offers a limited number of configuration options pre-programmed into the controller.
Fixed-function and configurable controllers are well-suited for applications like consumer electronics devices (i.e., a USB mouse) where the lifetime of the product is expected to be a few years at best and the product only needs to interoperate with a limited and well-defined set of other devices (i.e., PCs and laptops). However, fixed-function USB controllers can provide optimal quality for only a limited number of devices. Similarly, if the settings available on a configurable controller don’t match the particular device a user owns, then the quality of the user experience will drop. Interoperability issues like this only become more prevalent as specifications change.
In contrast, a programmable USB controller can maximize quality across devices and use cases by giving developers full access to the capabilities of the controller. Using feedback, it is possible for a controller to dynamically adjust and tune its settings to optimize performance with a particular device. In addition, if a new standard is introduced or unforeseen problems arise, the USB controller is flexible enough to address these issues through a firmware upgrade. This enables automotive OEMs to ensure that interoperation, quality, and reliability are maintained over the life of the vehicle.
It is important to note that developers do not need to program a controller directly to access its full capabilities. Instead of writing firmware, developers can use advanced development tools to define how the controller will operate. These tools then automatically produce the appropriate firmware. These tools also simplify the process for updating controllers.
Some USB controller manufacturers also take on the task of managing interoperability with new USB-based devices as well as accommodating specification changes. This frees automotive OEMs from having to dedicate engineering resources to perform these tasks themselves.
The truth is that automotive USB controller is not a commodity product. Consider that when a USB mouse stops working, it can be replaced for less than $10. If the USB port in a car stops working, it can be an expensive warranty repair to cover. Thus, USB controllers for vehicles have to meet higher standards all around. Yields have to be much higher than they are for consumer products. Electronics for automotive applications must be able to withstand much hotter operating temperatures. Finally, automotive components need to be available for longer than traditional consumer electronics applications require; i.e., commodity controllers may only be available for a short time, rather than the 10+ years needed by automotive OEMs.
Integration
One of the key challenges of designing a USB Type-C subsystem with higher power delivery is that the power source needs overvoltage, overcurrent, ESD, and short protection as well as high-voltage gate drivers. Cable compensation is also required to ensure signal quality over the long cable is maintained in a vehicle. To support reliable operation in the often confined and environmentally extreme operating conditions of a vehicle, temperature-based power throttling is necessary to prevent overheating and damage. Furthermore, OEMs will want to be able to support legacy USB Type-A devices during the transition to USB Type-C.
Circuit Protection: As a USB port is exposed to the real world, USB circuitry needs protection from a number electrical events. One of the most common is electrostatic discharge (ESD). For example, passengers moving around on vinyl seats or rubbing the carpet can build up an electrical charge. If they touch the exposed USB port, they can destroy sensitive electronics inside the car that are difficult and expensive to repair.
To protect against ESD, the system needs to be grounded to the shield ground so that the energy can dissipate safely. Ideally, the controller has integrated ESD protection. 8 KV contact and 15 KV air discharge protection is typically enough to protect the controller from ESD events. Additional ESD protection diodes can be added on the PCB board to enhance the protection further.
A USB port also needs protection from unexpected overvoltage (OV) and overcurrent (OC) events. A common instance of an OV and OC event can occur during device charging. To initiate charging, the device and power delivery system agree on a current and voltage to be used. However, if the system starts to supply the wrong voltage or current, an overvoltage protection (OVP) or overcurrent protection (OCP) circuit can trigger to protect the device.
Short protection is also necessary. When a cable is pulled out at an angle, it is possible for the Vbus pin to short to one of the digital pins momentarily. Given that Vbus can be up to 20 V and the digital pins are 5 V tolerant, such a short could destroy the affected port. Short protection is even more important for USB Type-C ports compared to USB Type-A. This is because the USB Type-C connector fits 22 pins (as compared to 9 pins for Type-A) into an even smaller form factor, increasing the chance of a Vbus short.
Ideally, short protection is integrated into the USB controller. Note that short protection is resettable so that the controller is not destroyed if there is a short. Instead, the controller shuts down to prevent the short. It can then be reset to restore the port, making a short event just a temporary and fixable issue rather than leading to an in-shop repair.
High Voltage Gate Drivers: To support backwards compatibility, the USB Type-C connector defaults to 5 V. Once the power delivery level has been negotiated, the controller may need to switch from a 5 V FET to a 20 V FET to support higher power delivery. If this capability is not integrated into the controller, additional circuitry will be required to drive the higher power FET needed to supply 20-V on Vbus.
Cable Compensation: For convenience, USB ports may be located throughout the car, such as in the front head unit, the center storage compartment between rear seats, and the glove box. For USB ports that support more than just power delivery (i.e., data functionality), the USB controller will likely be part of the infotainment system. To physically connect a port in the storage compartment to the infotainment system may require a USB cable up to ten feet in length. With such a long cable, there will be a significant voltage drop that can negatively impact signal quality and reliability.
To maintain signal quality within a reliable operating range, the controller can employ compensation. In simple terms, the firmware in the controller adjusts the output voltage to offset the voltage drop over the length of the cable. This compensation can be implemented as a fixed amount based on the length of cable used. Alternatively, the controller can dynamically compensate for voltage drops by regularly monitoring the signal it receives and modifying the compensation adjustment.
Temperature-based Power Throttling: One of the challenges of implementing USB Type-C is dealing with the extra heat dissipation associated with supplying up to 100 W. Overheating can cause a number of problems, including starting a fire and/or damaging the device being charged. Nearby components that are sensitive to heat, such as infotainment or navigation system electronics, could also be affected. Excessive heat dissipation may even damage the USB port itself, requiring an expensive service or warranty call to repair.
Temperature-based power throttling is an effective way to prevent overheating. Heat sensors located next to sensitive components alert the controller when the heat threshold is approached. The controller can then reduce the power being delivered. With less power, there will be less heat and the system can cool down. At the same time, the attached device can still be charged, just at a slower rate. This safety feature requires integration with the controller’s microprocessor and can be implemented in a manner that is transparent to users.
Legacy USB Type-A Support: While new devices will have USB Type-C connectors, there will still be billions of devices with USB Type-A connectors. Automotive OEMs will need to provide a USB Type-A port to support these legacy devices. Rather than implement two independent USB subsystems, controllers are available that can support both Type-A and Type-C ports. These integrated controllers simplify system design while minimizing total BOM cost.
Implementing each of these capabilities is necessary to ensure power source reliability and can substantially increase both the cost and footprint of the USB Type-C and power delivery subsystem within the vehicle. USB controllers for the automotive market have been designed to integrate these and other capabilities. This ensures components are automotive grade, work well together, keep costs down, and simplify design. Reducing the number of components that have to be assembled also increases reliability by reducing the number of points of failures.
Cypress has been a leading supplier for every generation of USB technology. With the EZ-PD USB-C CCG3P3 controller, automotive OEMs can bring the full benefits of Power Delivery 3.0 and Quick Charge 4.0 to their customers. The CCG3PA Evaluation kit provides all the support needed for designing USB Type-C power adapters/chargers and power banks, including firmware generation.
USB power delivery is quickly becoming a standard feature in vehicles. To maintain interoperability with next-generation portable devices, cars need to support the USB Type-C connector. The transition from USB Type-A to USB Type-C will introduce new capabilities, including faster charging. To maintain quality and interoperability over the lifetime of the vehicle, designers need a programmable controller that is flexible enough to support changes to USB specifications and interoperate with future devices based on these specifications. With the integration of key capabilities into controllers to protect internal electronics, OEMs can ensure reliability while minimizing system cost.
--
Mark Fu is a Senior Marketing Director of Wired Connectivity Division at Cypress Semiconductor Corp. Mark is currently responsible for product marketing and business development for Cypress’s USB solutions, focusing on USB-C and Super Speed USB. Mark has 25 years of experience in the semiconductor industry across multiple disciplines, including ASIC design, hardware engineering, design verification, application engineering, product marketing, and business development. Mark holds BSEE and MSEE degrees, and he is an author of two patents.
--
Subramanyam (Subu) Sankaran is a Sr. Marketing Director of Wired Connectivity Business Unit at Cypress Semiconductor Corp. Subu is currently responsible for product marketing and business development for Cypress’ Automotive USB-C Power Delivery Controllers. Subu has more than 20 years of experience in the semiconductor industry, spanning across applications engineer, technical marketing, product management, product marketing and business development. Subu has participated in the USB Standards definitions for USB 2.0/3.0 and USB-C. Subu holds Bachelor of Engineering and MBA degrees.