Mechatronic test benches ? Growing trend for validating control systems
January 17, 2017
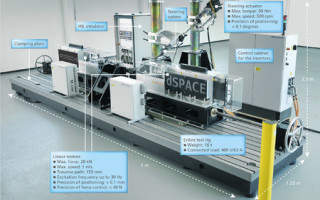
To validate complex vehicle control systems the mechanical components must be put to the test, which can be a time-consuming and expensive process. As automotive manufacturers look for more...
To validate complex vehicle control systems the mechanical components must be put to the test, which can be a time-consuming and expensive process. As automotive manufacturers look for more efficient solutions, there is a growing trend towards utilizing mechatronic test benches. Hardware-in-the-loop (HIL) technology has become the main backbone of engineering processes used to develop and test mechatronics.
To test mechatronics, engineers typically develop mathematical models that represent the mechanical components of a system under development. This is very cost effective and can be implemented significantly ahead of the mechanical systems or vehicles becoming available.
As system complexity has grown, however, mathematical models representing these systems have also become increasingly complex. Additionally, the system dynamics represented by the mathematical models can be very time consuming to compute.
While a slightly lower fidelity models may work in many cases, in complex safety-critical systems such as steering systems these models may not meet all of the development task objectives that engineering teams need to accomplish. Additionally, as more software is incorporated into modern electric power steering systems − particularly for advanced driver assistance systems (ADAS) and highly automated driving technologies − to support servomotors and driver-assistance functions, making these safety-critical vehicle components more complex. As a result, the scope and depth of testing requirements is also increased.
Combining mechanical components with HIL technology
To overcome the difficulty of modeling highly non-linear, fast system dynamics, engineers can combine many mechanical components with HIL technology. This combination provides the benefit of being able to test all possible high-risk boundary conditions in the relative safety of a lab environment, as well as the ability to validate mechanical system performance under dynamic conditions earlier than is possible by outfitting a production vehicle with instrumentation. With such a system in the lab, each test can be repeated for various software versions or even entire vehicles under the exact same conditions.
With these highly-dynamic mechatronic test benches, automotive original equipment manufacturers (OEMs) can test everything from a single electronic control unit (ECU) to entire vehicle systems while keeping high-risk road tests to a minimum. This means that manufacturers can efficiently test and optimize the behavior of a new system early in the development cycle, and, more specifically, that controller and functional software can be tested before vehicle integration – a step that typically occurs at the end of the development process.
Early testing is made possible by completely simulating real environments in which an ECU would operate. Open models are used to simulate the whole development process, from functional design to ECU testing, and any component (i.e. engines, vehicle dynamics, electric components, drivetrains, traffic sensors, etc.) can be modeled and combined to build an entire virtual vehicle for testing in a simulated environment. On the test bench, these models are used in combination with real controllers and real mechanical components in an HIL environment to run simulated experiments and observe component and system behaviors.
Simulating an electric power steering system on a test bench
Porsche is an example of an OEM that recently developed and validated an electric power steering system using a mechatronic test bench that included a HIL simulation system.[1] Seeking a more efficient way to manage its testing activities, the sports car manufacturer recognized that a mechatronic test bench was a viable solution for them as it could easily and accurately extend and reproduce tests, improving the overall efficiency of its testing processes.
Actuators are incorporated into Porsche’s test bench to mechanically stimulate the steering system, which makes it possible to test system behavior almost exactly as you would when test driving a real vehicle prototype. This enables Porsche to test new functions early on to identify important parameters and assess the limits of vehicle dynamics without risk.
By bringing part of its steering system testing into the laboratory, Porsche was able to achieve development efficiencies, says Anton Uselmann of Dr. h. c. F. Porsche AG at the Weissach Development Center in Weissach, Germany.
“Because it is highly dynamic, the mechatronic test rig from dSPACE is an important development tool for us that perfectly integrates into the highly demanding Porsche steering system development,” Uselmann said.
Common applications for mechatronic test benches
Mechatronic test benches are commonly used to test and develop functions, automate software releases, examine error-case behavior, validate concepts, complete mechanical endurance tests, and measure units under test. Some of the typical mechatronic test benches that incorporate HIL technology include:
- Steering systems, such as:
- Electric power steering
- Superposition steering
- Controlled electric pumps (e.g., fuel and hydraulic)
- Brake boosters
- 3-D motion platforms for vehicle dynamics control systems
- Mechanical loads for real pump motors
- Mechatronic ECUs with integrated sensors and actuators, such as:
- Gear control units with integrated speed sensors
- Parking brake ECUs with integrated inclination sensors
- Electronic stability programs (ESPs) with integrated rotation rate and acceleration sensors
- Pedal actuation for testing electric brake boosters
- Force feedback control in driving simulator applications
Test benches are also used for smaller applications, such as seat controls, fans, belt tensioners and electric tank caps.
“We are not afraid of the level of complexity that is associated with an application,” said Matthias Deter, Engineering Group Manager, dSPACE. “We work closely with our customers to meet and understand their specific requirements in detail. The customer’s requirements go directly into the concept of the test bench so that a customized, optimal solution is always the result.”
[youtube=https://www.youtube.com/watch?v=brV-JrDMa2o]
dSPACE Inc.
References:
1. “DSPACE.” DSPACE Magazine – dSPACE. Accessed January 16, 2017. https://www.dspace.com/en/ltd/home/medien/dspace_news.cfm.